By: Hassan Ali
Translation: Yousef Awad
Leatherworking is one of the oldest crafts known to humanity. People have long benefited from animal hides, whether from animals they consumed or other deceased creatures. These hides were transformed into clothing and shoes, providing protection against cold weather and the harsh elements of nature. In modern times, leatherworking has expanded significantly. It encompasses the production of shoes, bags, belts, and various other accessories needed for daily life.
We can define leather industries as “all products made from either natural or synthetic leather.” This includes leather clothing, footwear, bags, leather-upholstered furniture, artistic creations, and more. The ancient people of Palmyra excelled in leather craftsmanship. The leather shoes discovered in Palmyrene tombs, exhibited in the Palmyra Museum, serve as compelling evidence of their skill. Across generations, the people of Palmyra have preserved this craft, and it remained popular in the city until the significant displacement of its inhabitants in 2015 due to the invasion by ISIS.
Mr. Tareq Al-Skaf (whose nickname is derived from the profession of “Al-Iskafi,” meaning shoemaker), a 52-year-old shoemaker and leather bag craftsman from Palmyra, shares his insights: “Our ancestors relied on local animal hides from sheep and camels, or imported cowhides, to create a wide range of leather products. Some of the most well-known items include:
- Sharukh (Na’oul) Shoes: Designed for outdoor use.
- Babouj: Specifically crafted for home use, especially during winter.
- Sandals: Ideal for warm seasons.
- Khuff: Intended for cold weather.
- Jood (Zarf): Leather containers used to hold water or milk among the Bedouin.
- Leather Bags: Available for both men and women, as well as for carrying shepherds’ supplies.
- Horse Hoof Covers: Made either from leather or metal.
Wadah Al-Ahmad, shares insights about the craft of shoemaking and leatherwork in the city. He inherited this profession from his father, who, in turn, received it from his ancestors. This craft has roots dating back hundreds of years in Palmyra. His workshop was located in the southern market, known as the “lower market” or the “Orientals Market.” It operated within a selling stall. The primary type of leather they worked with was Awassi sheepskin, which was locally produced in Palmyra. They also imported other types of leather, such as cowhide and camel leather. The most significant products they crafted in Palmyra included:
- Traditional Palmyrene Shoes (Sharukh): These shoes are distinctive, featuring a leather cover for the big toe and another cover for the remaining toes, along with the foot. They are affixed to soles made from layers of Awassi sheepskin for comfortable walking.
- Palmyrene Clashes (Klash): These shoes have two pieces that cross in an “X” shape, covering the toes and attaching to the sole.
- Women’s and Men’s Slippers (Khuff): Crafted in the traditional Palmyrene style.
- Leather Bags: Both men’s and women’s bags were produced. Women’s bags were adorned with local silk thread embroidery along the edges, while men’s bags were typically left plain.
- Saddlebags (Adl): Used for horses and donkeys to facilitate riding.
- Belts (Zanarat) and Gun Holsters (Mujand): Essential for hunters and others.
During his displacement to Turkey, Wadah adapted his craft by using new tools, materials, and machinery that were not commonly used in Palmyra. He introduced modern shoe and bag designs, including electronic device bags (for mobile phones and tablets). Laser engraving and handcrafted embellishments became part of his repertoire. Additionally, he incorporated leather polishing techniques using creams.
Wadah Al-Ahmad, continues to share insights about the tools commonly used in the craft of shoemaking and leatherwork: In Palmyra, we worked with simple handcrafted tools, often obtained from local blacksmiths. These tools included:
- Scissors and Knives (Masharat): We used these tools to cut leather pieces according to the required measurements.
- Mallets (Madaqat): These were essential for shaping and molding leather.
- Anvil (Sandan): Made of brass by local blacksmiths, the anvil served as a base for various leatherworking tasks.
- Manual Grinding Wheel (Jalakh): Before electric grinding wheels became common, we used manual ones for smoothing and shaping leather edges.
- Sewing Machines for Leather: We occasionally acquired sewing machines specifically designed for leatherwork from workshops in Aleppo or Damascus.
- Silk Thread Embroidery (Khayt Al-Kharaza): This thread, also known as “Khayt Al-Sareed,” was locally produced in Palmyra from sheep intestines. We treated it with beeswax to prepare it for work.
Upon arriving in Turkey (specifically in Reyhanlı), I discovered readily available and more advanced equipment and tools in the markets. These modern tools significantly increased production efficiency and improved the quality of our craftsmanship. Additionally, online communication channels and search engines allowed me to explore new designs and incorporate them into my trade.
The income generated from this profession is somewhat satisfactory, provided there is a consumer market for these crafted goods. Currently, I sell most of my products to foreign markets, including Western European countries and East Asian nations.
Regarding training the younger generations in this craft, I currently have four apprentices. Three of them have special needs and attend daily for learning. I hope to expand the reach of this profession among young people to preserve it and prevent it from fading away.
The most significant challenge we face in this profession is sourcing the necessary raw materials, particularly leather. Previously, we found our required leather supplies in the markets of Antakya. However, after Antakya was devastated by destructive earthquakes in February 2023, leather availability there declined. I embarked on a multi-day journey to various cities in Turkey to search for raw leather materials. Eventually, we found what we needed in Istanbul’s markets, albeit at a higher price. Additionally, the steep shipping costs from Istanbul to Reyhanlı will be added to the challenge.
I sincerely hope that support for this project continues, along with backing for other traditional crafts. Our goal is to pass down these skills to future generations, ensuring they do not vanish into obscurity.
Photo annex
Figure 1: Image of a piece of leather from Awassi sheep after processing.
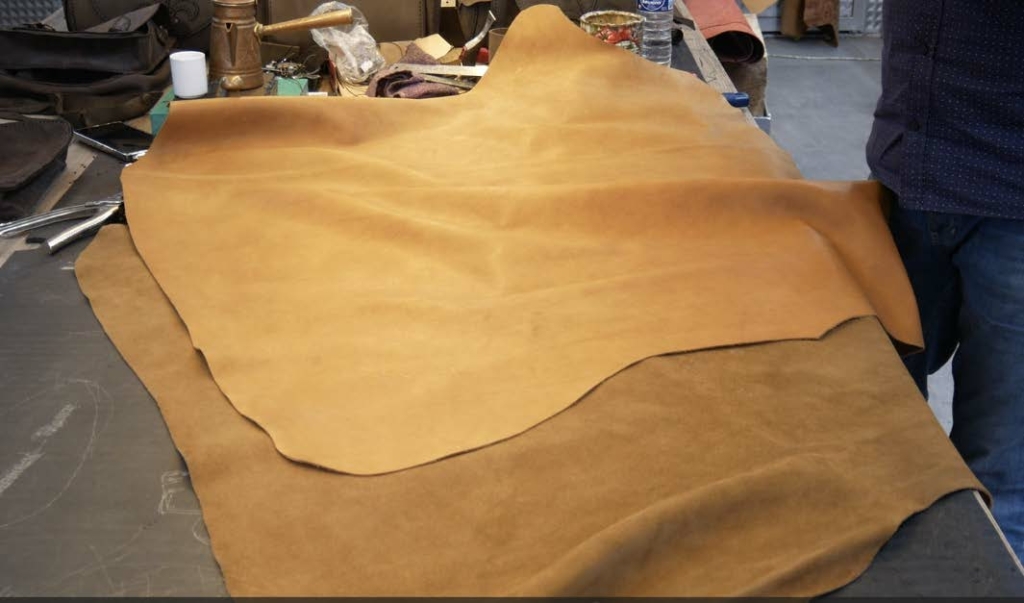
Figure 2: Image of a piece of leather from Awassi sheep after processing.
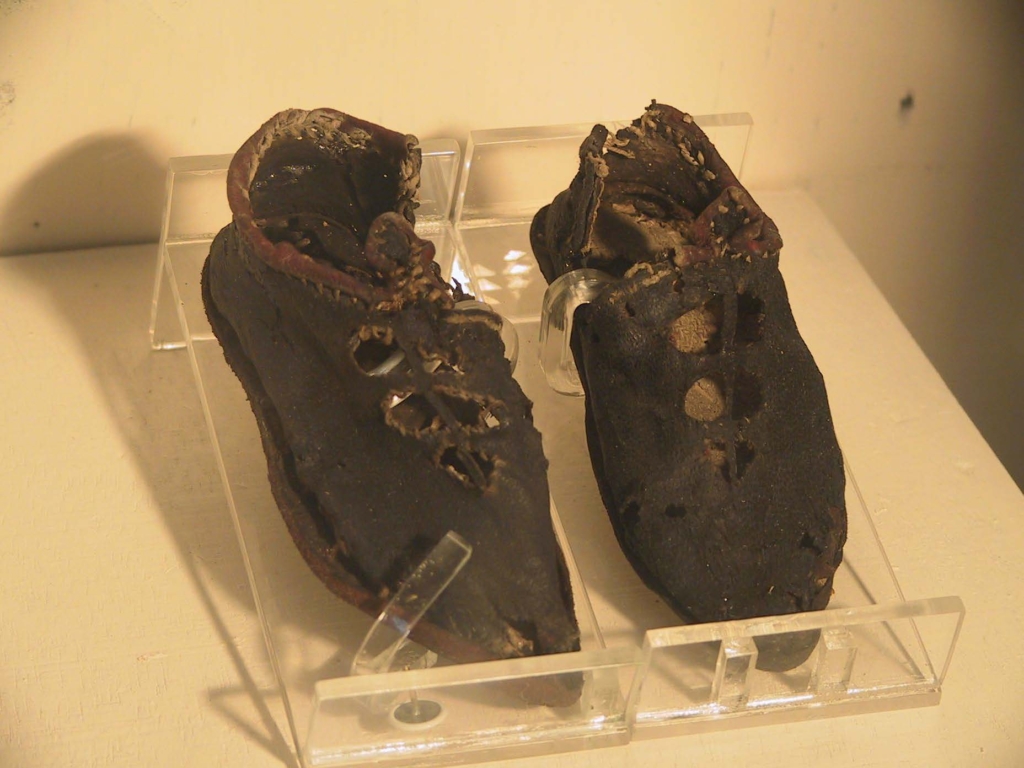
Figure 3: Image of a leather craftsman.
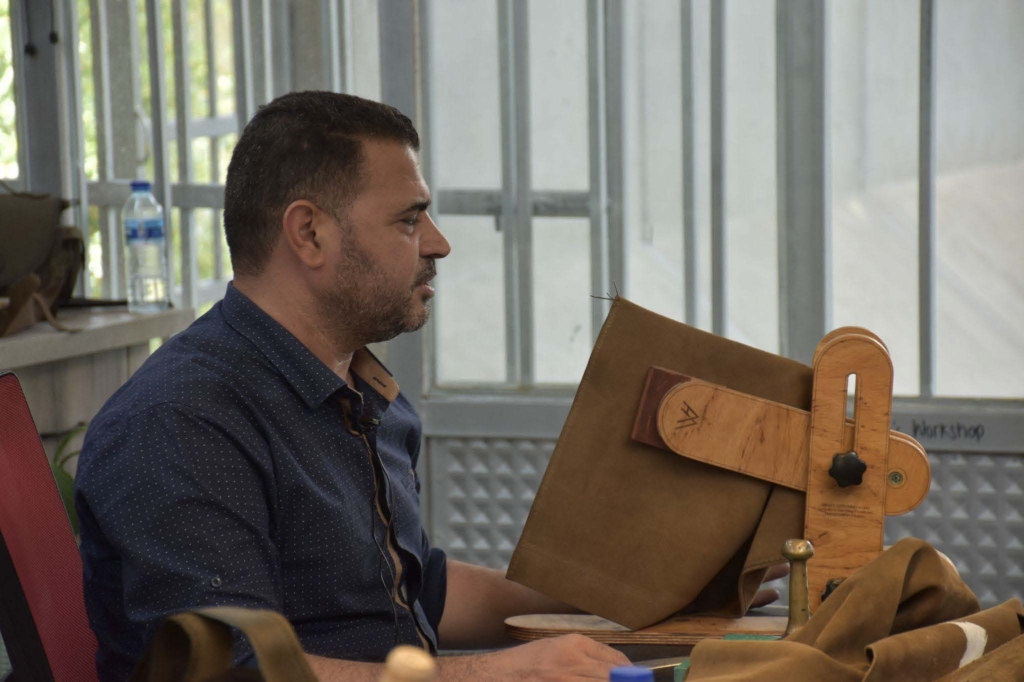
Figure 4: Image of a traditional Palmyrene bag.
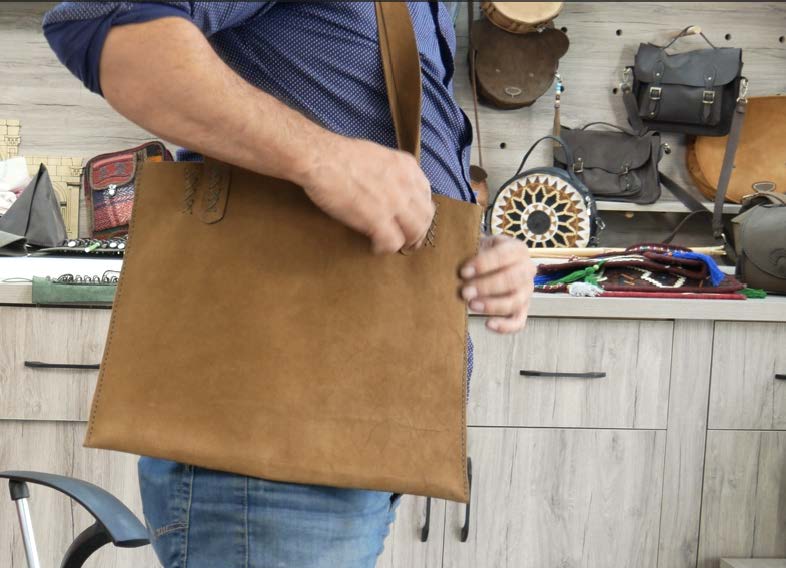
Figure 5: Image of a traditional Palmyrene shoe.
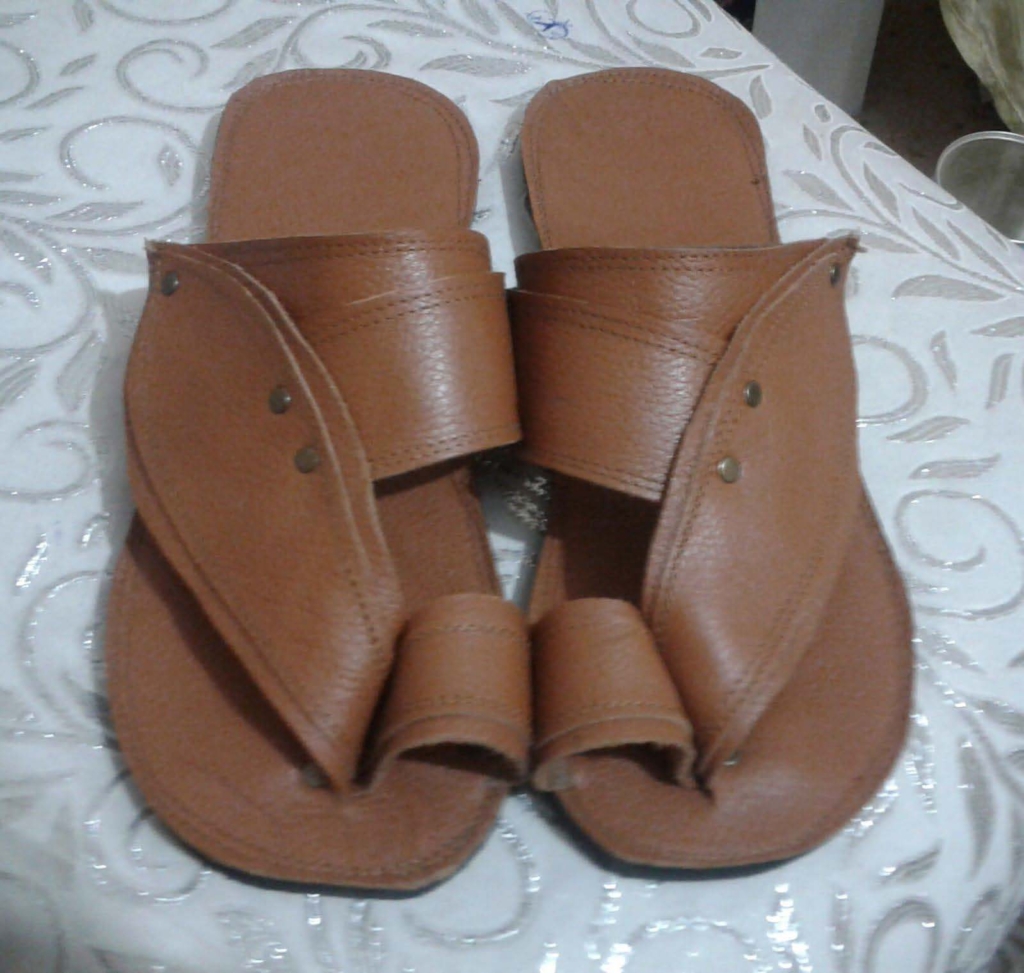